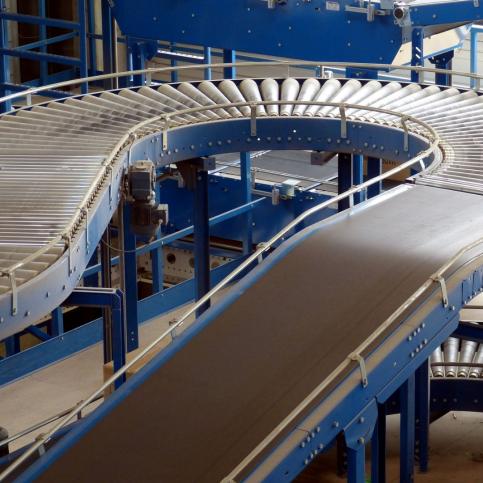
6 Factors To Consider Before Selecting A Gravity Roller Conveyor
Among the myriad conveyor systems in the market, gravity roller conveyors remain one of the most prominently used. Comprising rollers or wheels, these conveyors use gravitational force to transport objects. Primarily available in straight, curved, spur or merged configurations, they are an integral part of material handling in packaging, manufacturing and package distribution industries. However, before installing a gravity conveyor, a few factors need to be taken into consideration. These factors will be examined below in detail.
Factors determining roller conveyor selection
Dimensions and weight of smallest/largest load
Determining a gravity roller conveyor is a step-by-step process. The preliminary step is to calculate the weight and dimensions of the largest load and the smallest load that will be transported on the conveyor. Once this is ascertained, other factors such as the spacing between two consecutive rollers, their diameter, and the width of the frame and floor supports can be determined.
Axle Centre
Axle centre can be defined as the distance between the centre of two adjacent rollers in a conveyor. In a gravity roller conveyor, at least three rollers should be in contact with the bottom of the package at all times. This ensures a seamless movement of the load without creating excess vibrations. Thus, depending on the weight of the load being transported, the axle centres might need to be reduced even further to ensure even weight distribution.
Diameter of individual roller
The next factor to consider is the diameter of the individual rollers and the size of the axles. Smaller and larger diameters each have their own pros and cons. While smaller rollers are economical, their load-bearing capacity is limited. Hence, heavier loads will require the use of larger rollers and axles. The thickness of roller tubing will also need to be taken into consideration while manufacturing rollers. Depending on loading conditions, thinner or thicker tubing is recommended. For instance, if packages are loaded onto the conveyor via forklift or dropped from a height, then it will require a thicker gauge of tubes to prevent rupturing.
Between frame width
This is the width between the two parallel rails on a conveyor frame, measured from the inside. Depending on the placement of rollers with respect to the rails, the BF width can vary. If the rollers are placed high above the rails, then the package can exceed the width of the frame as long as it is stable and free from collisions. However, if the rollers are recessed, then the width of the package can’t exceed BF width. In such cases, this width is calculated by adding 2 inches to the width of the largest package that will be transported using the conveyor. Apart from the placement of the rollers, the trajectory of the conveyors will also define BF width, as curved conveyors will require more width to transport the package safely.
Frame Material
The frame will not only support the load being transported but the conveyor itself. Hence, the frame material will need to select as per application. If easy installation and light load transportation are required, then aluminum frames are ideal. However, if the packages are heavier, then it's better to opt for a steel frame.
Use of floor supports
Typical floor supports come in either H-shaped or tripod configurations, depending on the permanent or temporary nature of the installation. Installed at the bottom of the frame, these supports generally have variable heights.
Gravity Roller Conveyors Supplied By Norpak
Norpak Handling has a wide range of Hytrol gravity conveyors divided into three main sections: light, medium, and heavy duty. The features of a few models from each category will be discussed below:
Straight Lightweight Gravity Roller Conveyor- SSR / SAR
Features:
- 1 ⅜ inch diameter rollers. Perfect for light material handling operations
- Has 6 roller centres
- Can be installed with aluminum or steel frames
- Can bear a maximum load of 45 lbs per roller on steel frames, and 30 lbs per roller on an aluminum frame
Medium Duty Gravity Roller Conveyor - 19GSR / 199SR
Features:
- Rollers with a diameter of 1.9 inches and varying gauges
- 19GSR has a maximum capacity of 210 lbs per roller, whereas 199SR has a maximum capacity of 250 lbs per roller
Curved Heavy Duty Gravity Roller Conveyor- 25SR/25SRC
Features:
- Bigger, 2.5-inch diameter rollers with varying gauges
- Curved frame to add more width and versatility during material handling operations
Straight Heavy Duty Gravity Roller Conveyor- 36SR
Features:
- Designed for pallet handling operations
- Can carry as much as 1017 lbs, depending on the model and the between frame width
Conclusion
To know more about other gravity conveyors and customized material handling solutions, reach out to us at Norpak Handling. We will be happy to provide extensive consultations in order to ensure you choose the best conveyor system for your particular operations.